Advantages
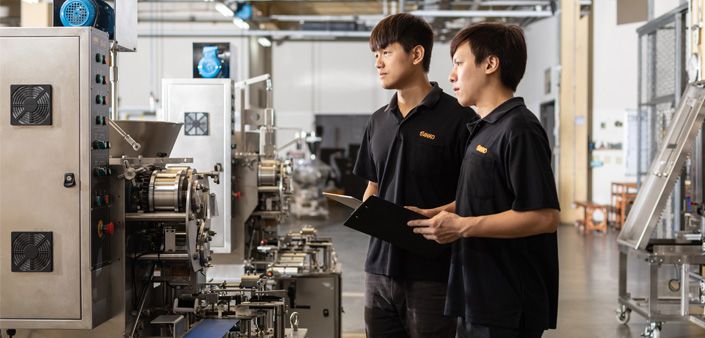
We have accumulated years of international experience and a wealth of international expertise.
We have sold our products in 114 countries, with experience in making over 700 types of ethnic food products
With over 195 countries around the world, ANKO’s machines are now used in manufacturing factories in 114 countries. Food made by ANKO’s food machines is served in more than half of the world’s countries. If you have the opportunity to travel to these countries, why not take a look at the supermarket freezers and try to identify which food product is produced by ANKO’s food machine?
Local people know best about local traditional food. We actively recruit professional agents from all over the world.
Worried that Taiwan’s ANKO Food Machine can't replicate your local taste? ANKO has partnered with distribution agents in countries in Asian, the Middle East and Europe. We actively recruit professional food machinery agents from all over the world to provide you with accessible local services. For example, our agents in India can provide you with details for making rasgulla and Samosa; our agents in the Middle East will tell you the secrets to making good kubba and falafel; and our American partner will share with you the best recipe to make the burrito and pupusa. All of this knowledge is part of ANKO's professional services. (Click for more information on agencies >Click here)
ANKO understands how to overcome differences in local raw materials and perfect the recipe
Ethnic foods in different countries use different local ingredients, including a wide array of flour varieties. How should we adjust the softness of the product to facilitate machine production according to the water absorption rate and the gluten content of each variety, and best match the local taste? ANKO owns a global food recipe database. Even if you don't have any experience in food production, as long as it is a common ethnic food, we are confident that we can provide you with a food recipe for success.
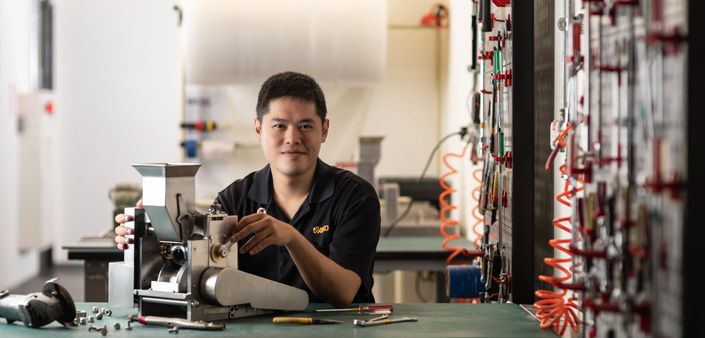
From soft knowledge to hardware devices, ANKO strives to meet your requirements
Modularized customized mechanism will better meet your production needs
The biggest feature of ANKO Food Machine is to provide module customization services. There are many functional key parts and molds that can be customized. For example, HLT-700XL's exclusive molds produce more than 300 customized products. ANKO Food Machine can speedily produce samples according to customer's product characteristics, recipe, shape, size, weight and other special requirements using the prototype machine, and simulate the actual production machine for testing. Once the customer expresses satisfaction, we develop the formal mold to complete the ideal product.
For newcomers or factory expansion, ANKO offers stand-alone machine to factory planning consultancy services
ANKO can assist in designing production lines according to customer needs, provide comprehensive whole plant solutions and equipment for plant planning, raw material processing, production line planning, production process optimization, as well as new product development and customization. ANKO is responsible for production arrangement, inspection, loading, on-site installation, training and after-sales services, significantly saving customers’ communication time from search for different machine manufacturers. It also allows customers to save cost including integration costs, transportation costs, and labor costs for separate machine installation. ANKO provides a single window for comprehensive after-sales services to prevent the risk of interruption in production.
ANKO not only understands the food machinery market, but also provides you with the latest recommendations on food market trends.
With over 47 years of experience in the food machinery industry, ANKO is familiar with the market and industry conditions. ANKO can help you make decisions and provide recommendations for industrial upgrades thanks to our decades of accumulated market information and food development. We want to provide customers with the latest and most valuable information, and send the latest food trends or updates to ANKO's monthly newsletter subscribers from around the world, so we can all progress together as one in the food industry. (Click to subscribe to the newsletter)
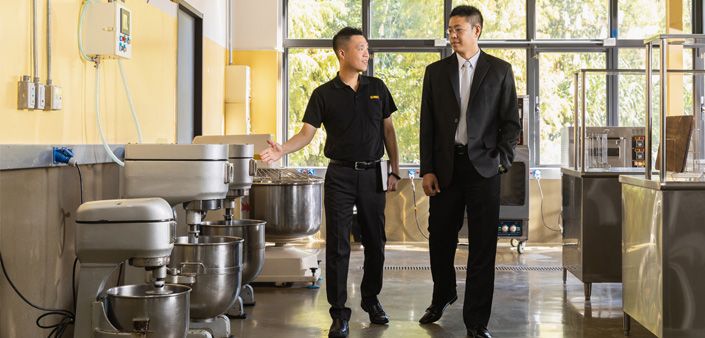
Comprehensive pre-sales and after-sales service, purchase the most suitable and satisfactory equipment
See details on our official website, FB, YouTube, Alibaba, with 24 hours standby feedback
The biggest concern when purchasing important equipment is unavailable service. At ANKO, our service goal is for all customers to receive our messages accurately and in a timely manner. Whether it's from ANKO’s official website, business and social platforms, you will be able to access detailed information on ANKO products and services. If you wish to further inquire about machine details or business advice, you can send messages or make calls directly through these platforms. ANKO will reply within 24 hours (excluding holidays) and provide you with the most appropriate solution in accordance to your product needs.
High-standard food lab to ensure that the food tastes exactly as you wished
The ANKO factory has a machine demonstration area as well as a bright and clean high-standard food lab which provide a variety of flours, seasonings, fillings, additives and various food processing equipment such as mixers, vegetable cutters, hydro extractors, steamers, ovens and other kitchen utensils. After assessment by our professionals, a machine trial will be arranged based on your needs. You can test recipes and machines to ensure that the ANKO equipment meets your actual needs and requirements.
Pre-shipment testing services for quality assurance
ANKO Food Machine Co., Ltd. guarantees consistent quality in each and every one of our machines. To ensure that each machine is delivered in perfect condition to our customers, we offer pre-shipment testing services for our customers. We inspect and fine tune the machine according to our customer's product type to ensure product quality.
Special wooden box packaging ensures that the machines arrive in good condition
After the machine is completed, it will arrive via land, sea or air transport. Heavy goods such as machinery requires heavy duty wooden box to prevent rupturing and damaging the product during land, sea or air transport. ANKO's packaging wooden box adopts a double pallet design to increase the load strength. The wooden panels are fixed with cleats, and the interior is reinforced by adding beams and columns. All strengthening measures are in line with international regulations to effectively protect products from damages during transport.
Simple and easy machine operations, provides instructions to ensure production quality
All ANKO machines use electronic screens or button control panels to provide intuitive operations. The way to operate machine is also pivotal to production quality. Therefore, implementing good training is also imperative at ANKO. After completing the purchase, you will obtain a detailed operation manual containing all the key points and precautions for machine operation. In addition, ANKO also provides customers with on-site training services regarding machine tuning and operation to ensure that customers do not have to worry about machine operation problems.
High-efficiency online/offline after-sales repair service, managed according to complexity
If any problems occur during machine operation, ANKO's service personnel will assist you every step of the way to eliminate the cause of the malfunction and reduce downtime. Based on the level of machine operation and damage, whether it is parts delivery or machine maintenance, we will provide different solutions according to the level of complexity, such as multimedia online tutorial and video, on-site inspection or return-to-factory maintenance services. We will choose the most time-efficient and cost-effective solution for you to solve your machine problems.
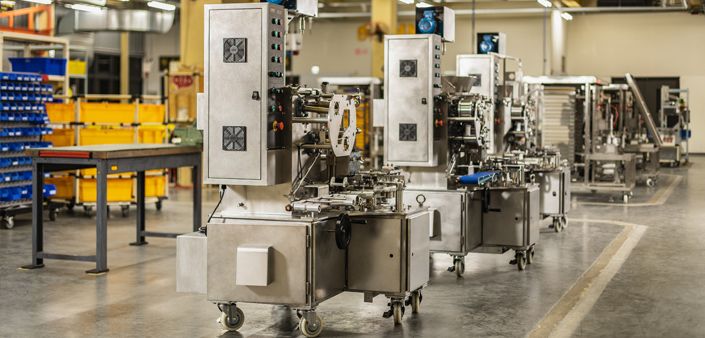
Stringent production SOP execution, never missing a delivery deadline
Introduce system management and electronic management processes to optimize material management
ANKO’s manufacturing capacities have always stayed competitive since our founding in 1978. We have successively introduced ERP, PDM and other electronic management systems to enhance material management, process management and control. The complete list of parts and versions of various machines are precisely controlled by ERP, PDM and other management systems to optimize production and after-sales service efficiency.
Approved quality with ISO and D&B world-class certificates
ANKO has a thorough and rigorous SOP, with solid vertical organization and fluid horizontal communication. It has passed the ISO9001 certification and is in line with international production standards and service quality. ANKO also has the D&B certification, which is an internationally recognized corporate reputation certification.
Quality parts suppliers and safety stock of spare parts
ANKO meticulously selects trustworthy and excellent part suppliers to ensure our ability to provide and deliver high-quality machinery and service to our clients. Our in-house "Procurement," "Research and Development," and "Quality Control" departments collectively assess each supplier based on four main criteria: "Production Stability," "Quality Control," "On-Time Delivery Rate," and "Pricing." A vendor evaluation along with an optimized supply chain system screening is conducted annually to help reduce uncertainties in the process and eliminates potential risks. Concurrently, we closely monitor the safety stock of parts and utilize procurement plans for essential components to ensure efficient delivery of parts and services for our clients.
Project management on the production schedule of each machine for both quality and progress
Immediately after the order is established, a dedicated "production line schedule control table" is constructed before starting the production SOP, thereby conducting precise regulation from parts procurement, mechanical assembly to quality inspection processes. Throughout the production inspection process, all quality control items are executed according to the “machine inspection record sheet”. The record will be stamped after completing the inspection to ensure quality for all machines.
Strictly abide by professional procedures and regulations throughout the year. Efficient, high quality production
ANKO has dedicated storage locations in the plant for materials and parts, semi-finished products or production tools. The on-site operation is based on the "5S Management Law": SEIRI, SEITON, SEISO, SEIKETSU and SHITSUKE (sort, set in order, shine, standardize and sustain) methodologies. The first priority is to improve production efficiency and maintain product quality. The maintenance of machinery and equipment during the production process shall be carried out in accordance with the “Environmental Maintenance Procedures” to ensure that the production and sales process is not affected by adverse environments and equipment. The assembly and inspection process is controlled according to the “Quality Inspection Control Procedures” to ensure operation and product quality.
We look forward to working with you as an ANKO customer. Please find the most relevant machine and fill in the inquiry form. We will contact you as soon as possible. Start now >
Need support?
Search for a topic or pick one below. We'll find you the best support options.